Precision Converting and Die Cutting
Exploring the Versatility of Precision Converting Processes at PLITEK®
PLITEK® offers a diverse range of precision converting processes, each tailored to meet the unique demands of our clients’ projects. Our primary cutting methods include rotary die cutting, flatbed die cutting, laser cutting, knife cutting, and hybrid processes – a combination of several methods for optimal results. Our dedicated engineering and manufacturing teams ensure that every customer benefits from our efficient and accurate precision converting processes.
Comprehensive Precision Converting Solutions
- Rotary Die Cutting: Ideal for high-volume production, rotary die cutting delivers consistent, high-quality results with tight tolerances. This method is well-suited for continuous rolls and can handle complex geometries with ease.
- Flatbed Die Cutting: This versatile technique is perfect for smaller production runs or applications requiring flexibility. Flatbed die cutting offers the capability to handle various material thicknesses and shapes, making it a valuable tool for custom projects.
- Laser Cutting: For applications demanding intricate details and precision, laser cutting provides a high level of accuracy. Laser cutting method is particularly effective for materials that are challenging to cut with traditional methods, offering clean edges and minimal material waste.
- Digital Knife Cutting: Known for its efficiency and flexibility, knife cutting is used for cutting softer materials and achieving specific shapes and sizes. It’s a great option for applications requiring a balance between precision and speed.
- Hybrid Processes: Combining multiple cutting methods, hybrid processes are tailored to achieve optimal results for complex projects. By integrating techniques like rotary and flatbed die cutting or laser and knife cutting, we can handle a wide range of material types and complexities.
Tailoring Precision Converting Processes: PLITEK®‘s approach
Our team understands that selecting the right cutting or converting process for an application is a nuanced decision that hinges on several critical factors. Our approach is to carefully consider each aspect to ensure the most efficient and effective outcome for our clients.
Key Considerations in Precision Converting:
- Production Volume: The scale of the project influences the choice of method. For high-volume production, rotary die cutting and hybrid processes are preferred for their efficiency and cost-effectiveness. For smaller runs, flatbed die cutting offers the flexibility needed for quick adjustments and customizations.
- Tolerance Requirements: Achieving precise tolerances is crucial for many applications. While rotary die cutting generally offers tighter tolerances, hybrid approaches like machine cavity punches or chemically etched plate dies can achieve extremely high precision.
- Material Type and Thickness: Different materials and their thicknesses impact the choice of precision converting technique. Our precision converting methods are designed to handle a variety of materials, from flexible films to rigid substrates, ensuring the best outcome for each specific material.
- Complexity of Lamination and Geometry: Projects involving complex lamination, intricate geometries, or multiple layers require careful planning. Our team expertly manages these complexities to ensure accurate registration and integrity of the final product.
- Slug Removal: Efficient slug removal is vital for maintaining production speed and reducing waste. Our processes include options for in-line or offline slug removal, optimizing efficiency for high-volume applications.
Customized Solutions
At PLITEK®, we understand that each project is unique. Our commitment to quality means we offer customized solutions tailored to customer specific requirements. Whether you need high-volume roll form, precise piece or sheet form, or specialized pouch packaging, we offer the expertise and flexibility to deliver the right solution. Additionally, our team collaborates closely with you to understand your project’s requirements. Moreover, we make recommendations that maximize both performance and cost-effectiveness.
Our team works closely with our customers to understand your project’s requirements and provide recommendations that maximize both performance and cost-effectiveness.

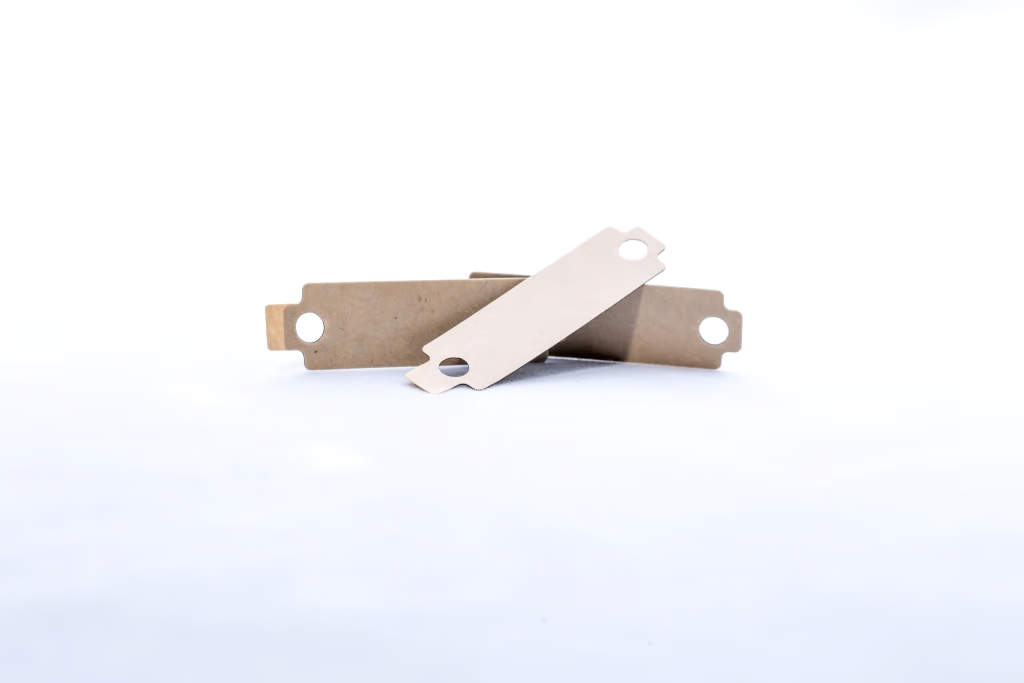
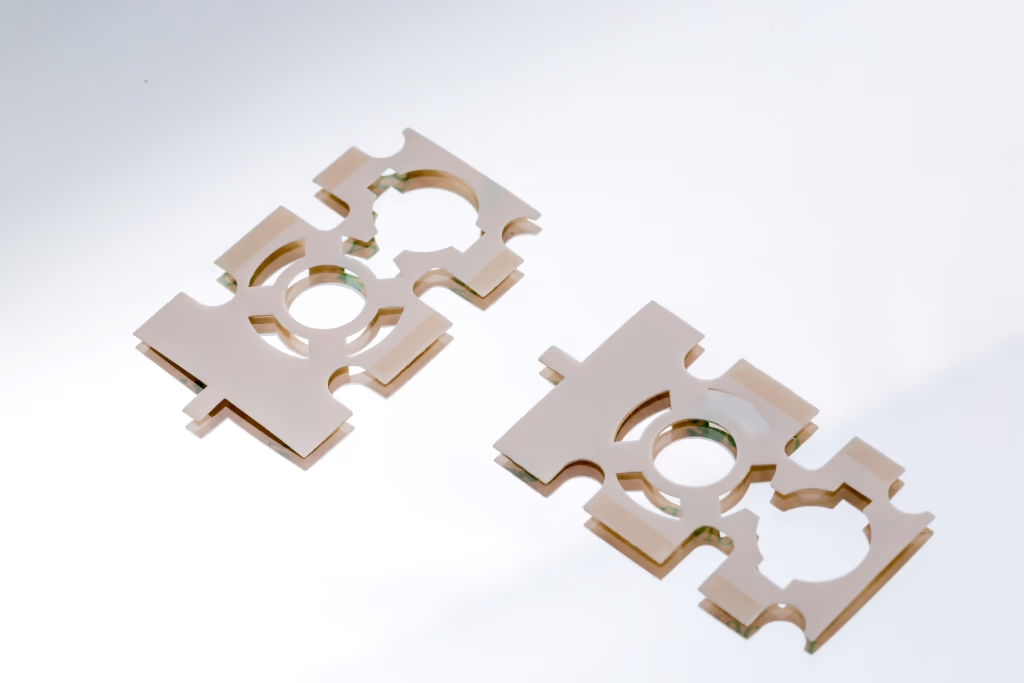